Team
Kaia Ambrose- Packaging Scientist
William Davis- Industrial Designer
Spencer Raymond Smith- Graphic Designer
Jacklyn Czapla- Graphic Designer
Role
Branding
Messaging
Book Design & Layout
Deliverables
Brand Identity
Packaging Design
Concept Imagery
3D Form
Process Book
When our team first decided to focus on prescription pill packaging for the Paperboard Packaging Alliance Student Design Challenge, it was because of our own personal experiences. Despite being rather young and healthy, struggling to open prescription bottles and blister packs was nothing new. Once we started to think about our grandparents and the elderly community as a whole, the conclusion was that there was an opportunity to better people's lives.
We also noticed that prescription pill packaging has not changed in almost six decades since child-safe packaging became popular in the 1960s. And so we felt like it was time to challenge the standardization of the prescription pill bottle.
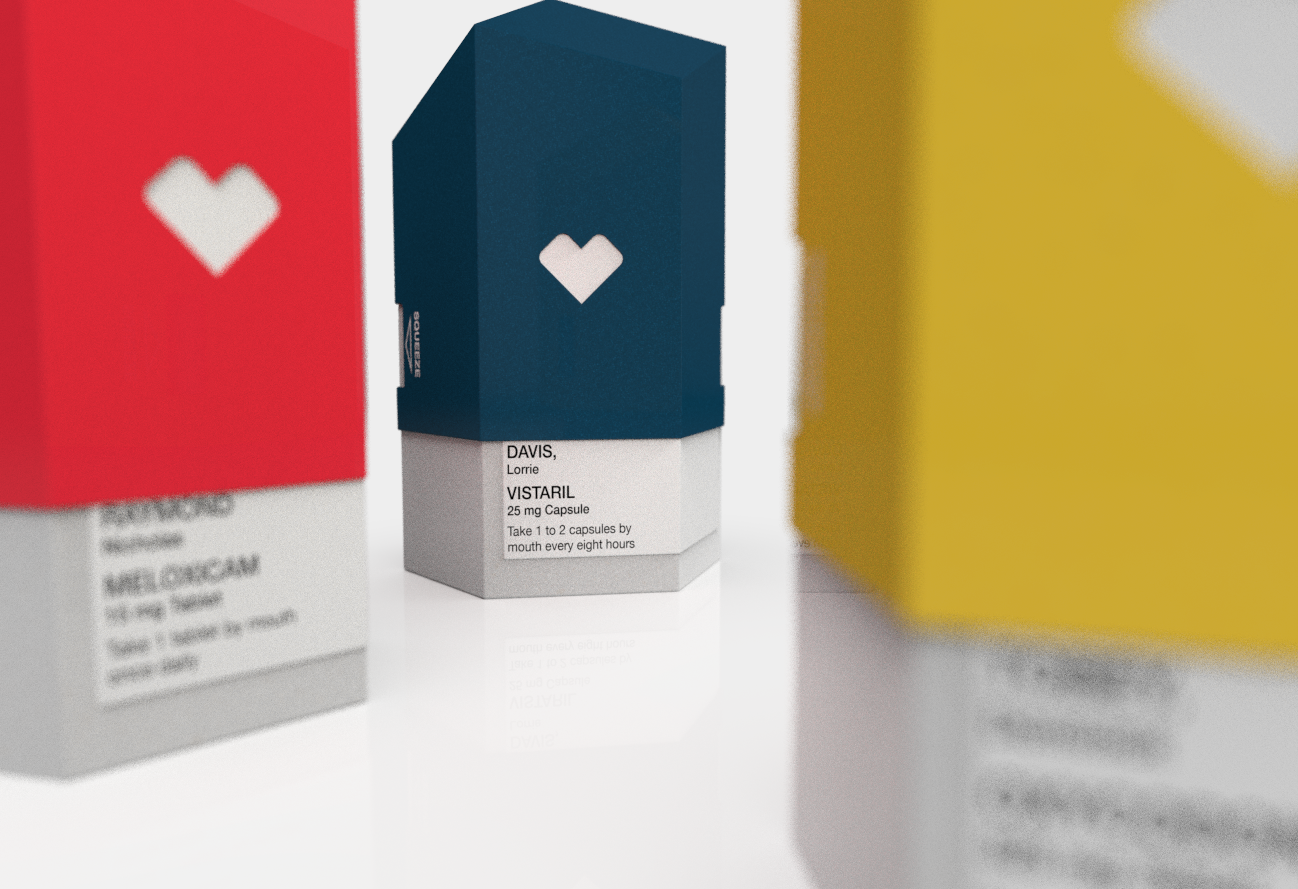
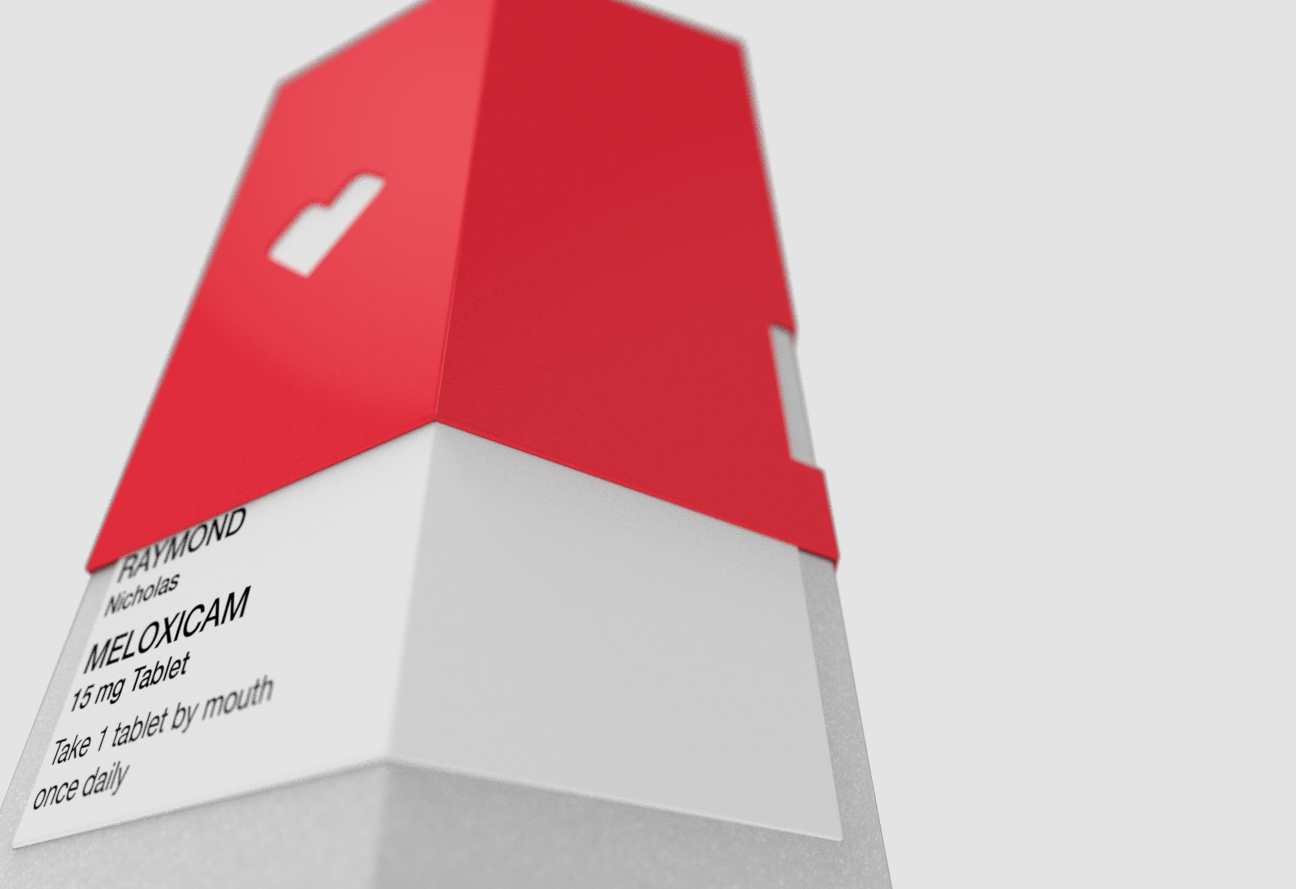
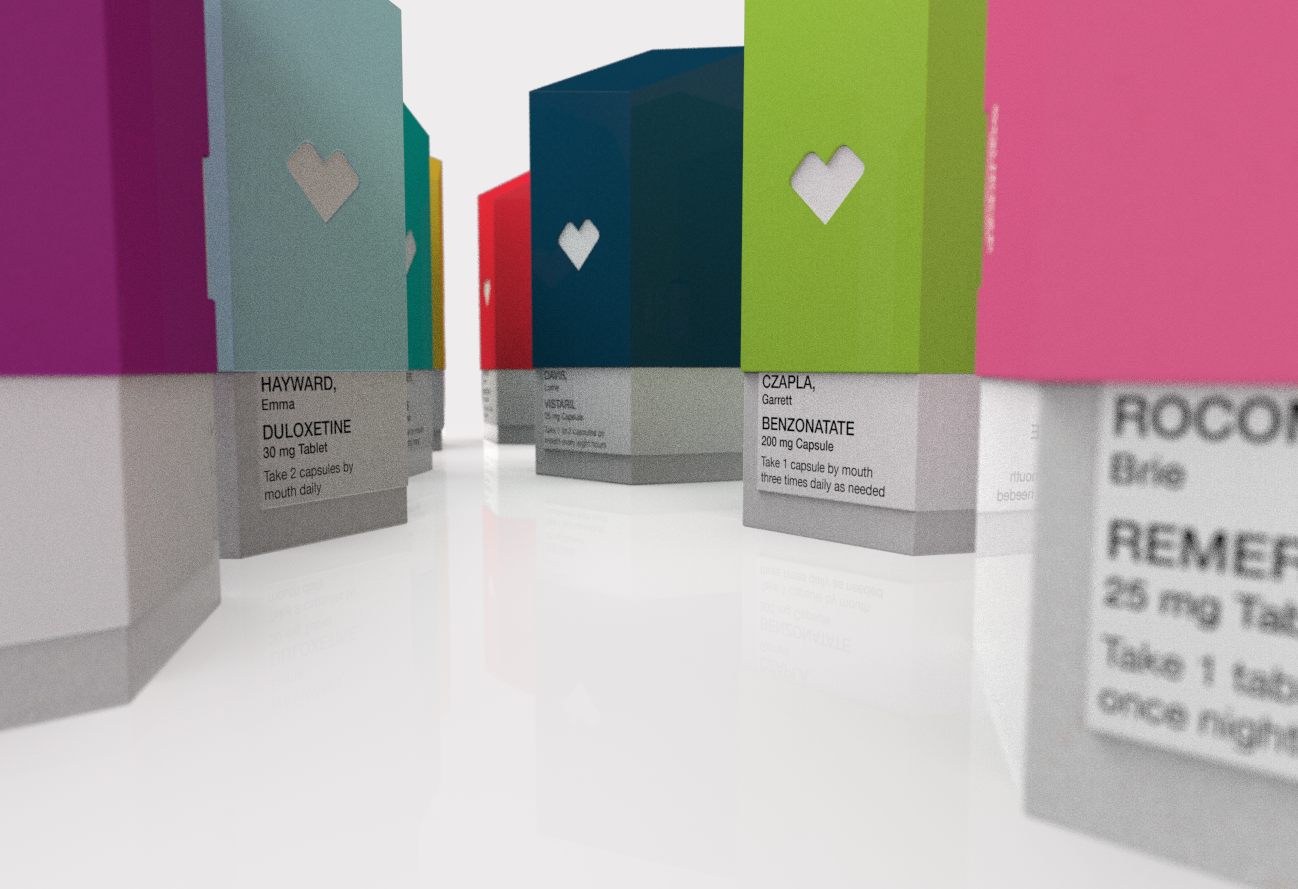
The Container
The main container is a hexagonal prism with three rhombic panels at the top and an auto-bottom. One — indicated by a small tab — opens while the other two are held in place by adhesive. A small hexagonal insert with panels slides in for additional stability and to catch granules that may result in long-term use. A sleeve similar in shape slides over the upper two-thirds of the main container, providing an additional layer of protection against the environment. Having somewhat large and flat faces aids in displaying all information required by regulations.
.............
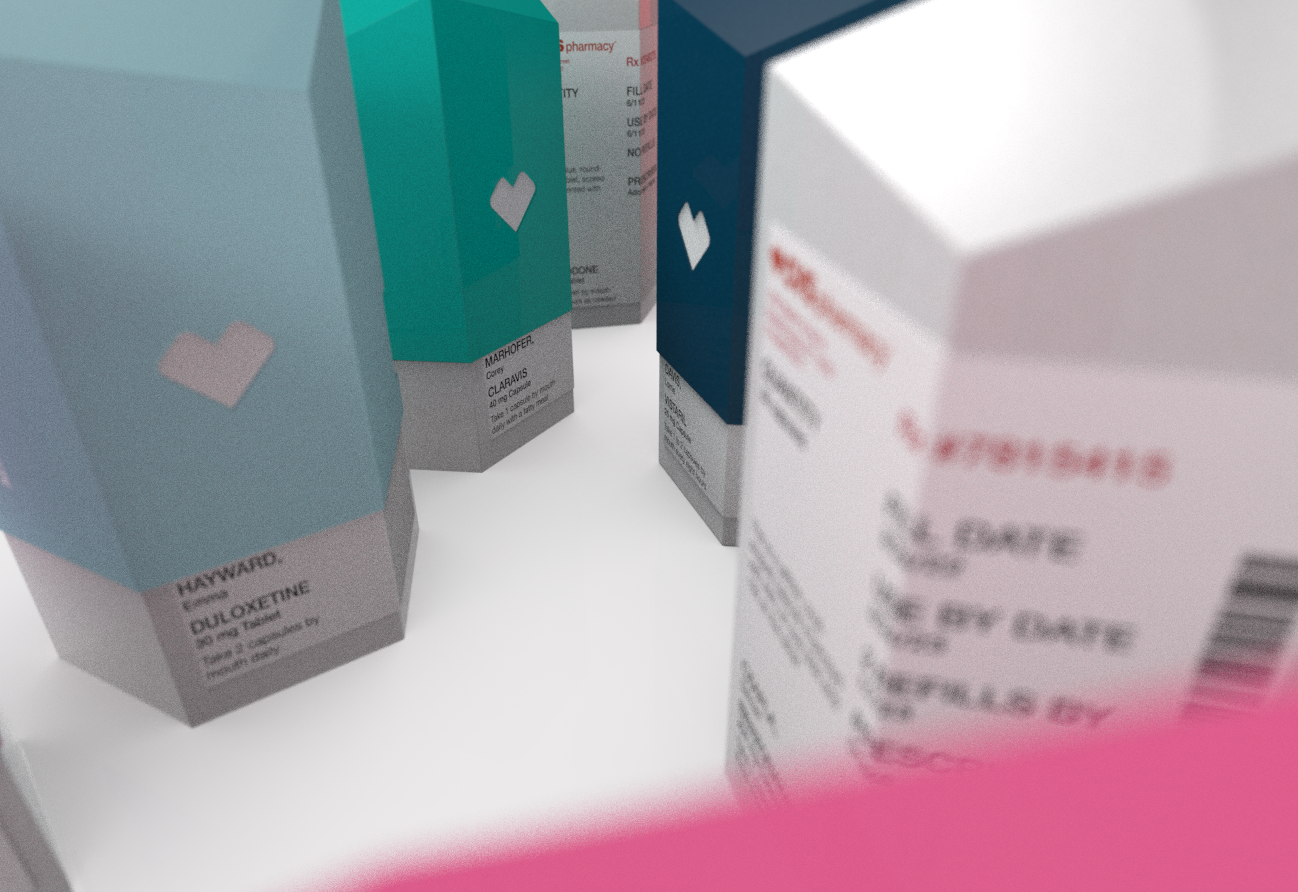
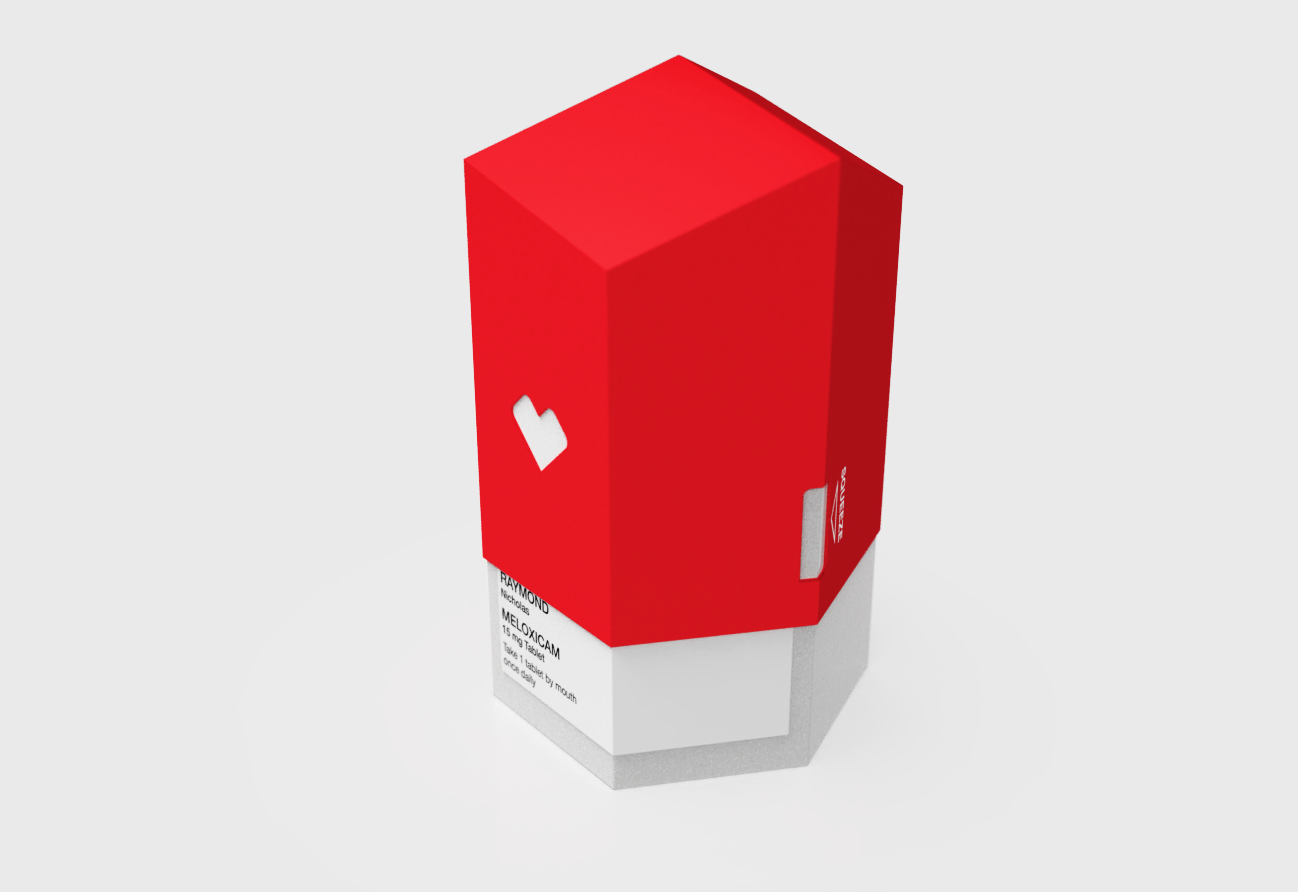
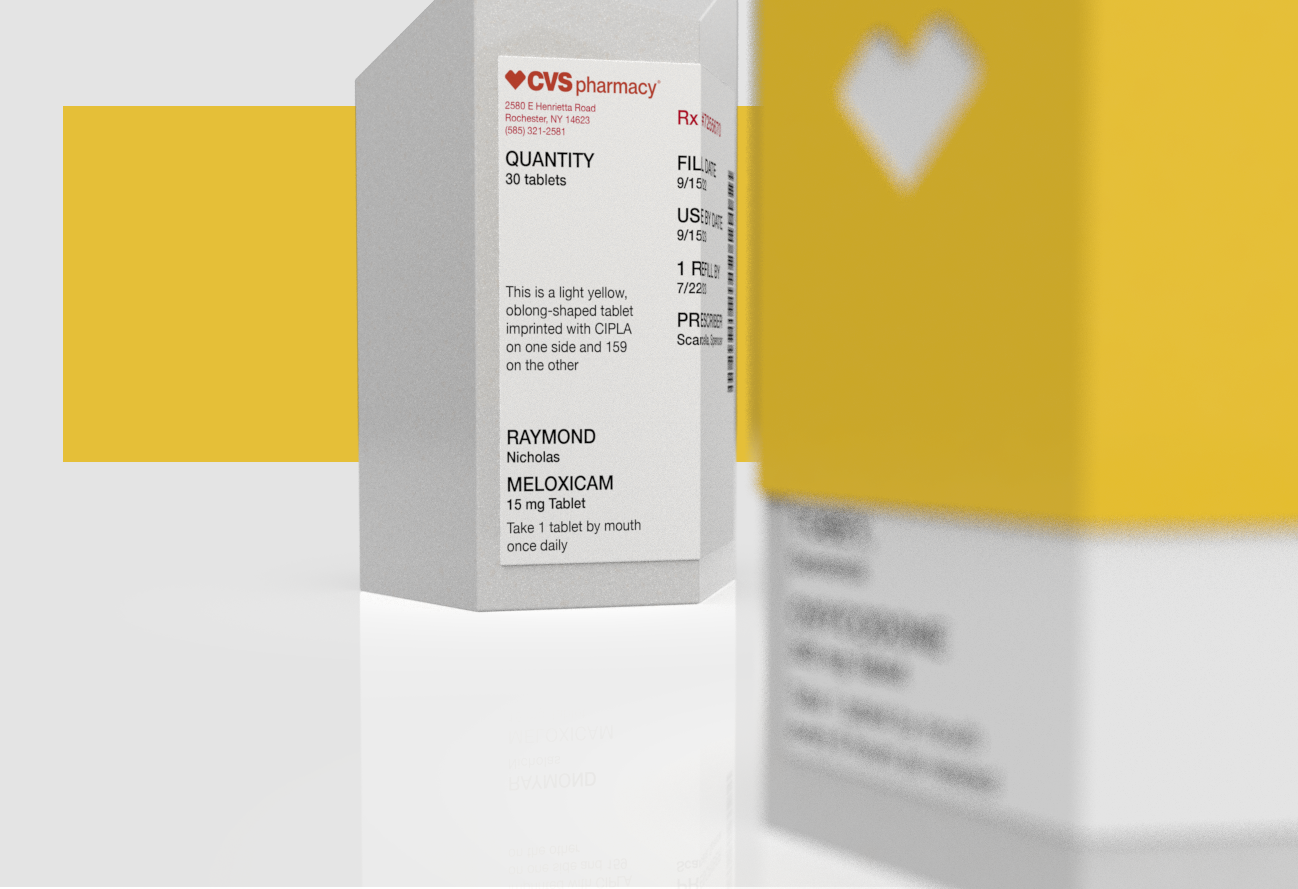
Child-Proofing and Contamination
A tight friction fit is used to prevent ease of lifting. Only when the sleeve is squeezed at pre-creased portions of the main container will it open. In the first five minutes of testing, only one child was able to access the container contents. After being shown how to remove the sleeve, only two more failures occurred, bringing the failure rate to 8.8%, well below the allotted 15% failure rate.
For prescription pills, prolonged exposure to microbes, oxygen, water vapor, and light is a concern, so a complete closure is a must. By selecting PET-laminated SBS paperboard, the carton remains resistant to oxygen and water vapor, while still being recyclable as over 95% of its mass is paper.
.............
Initial Paper Prototypes
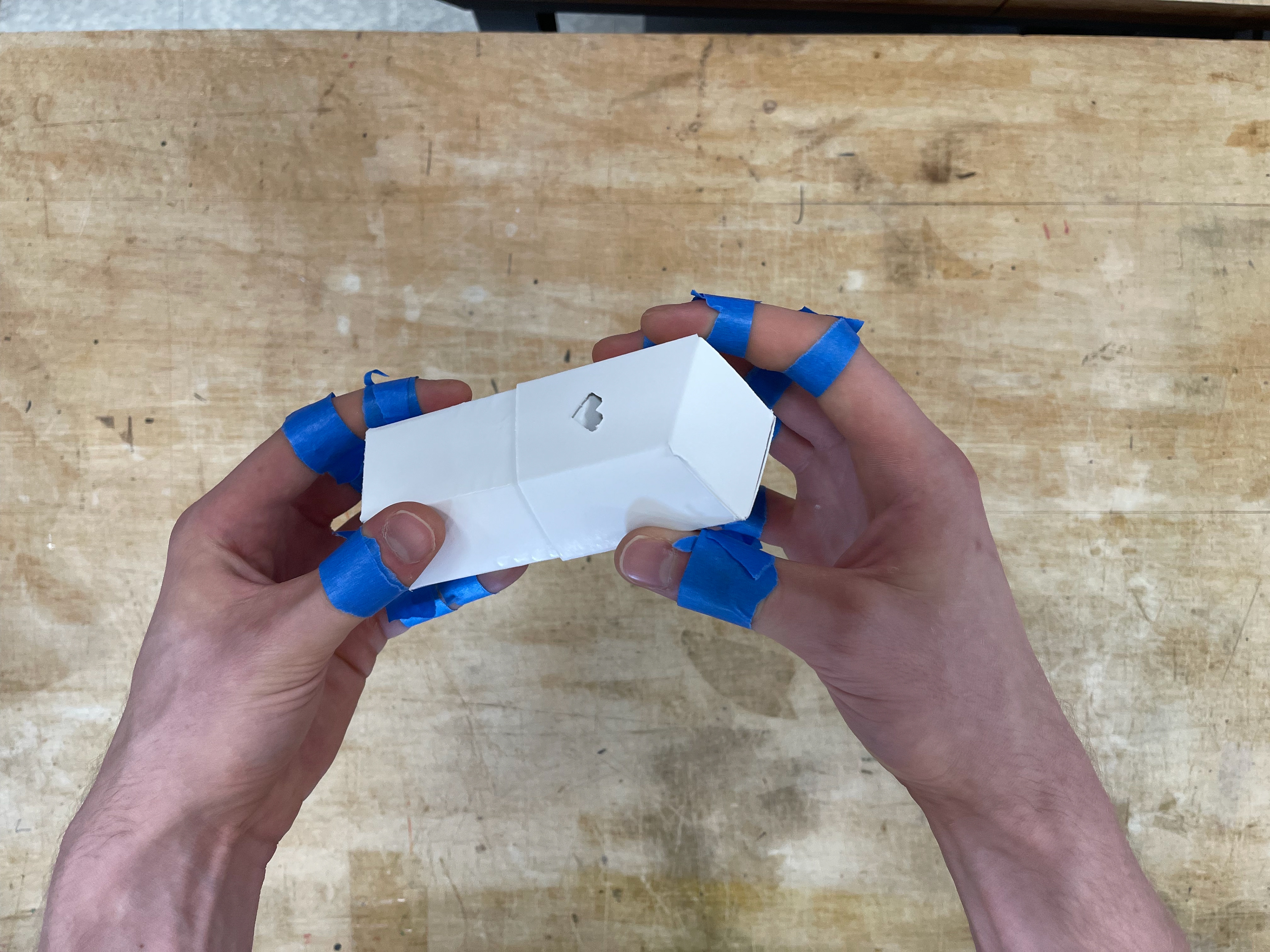
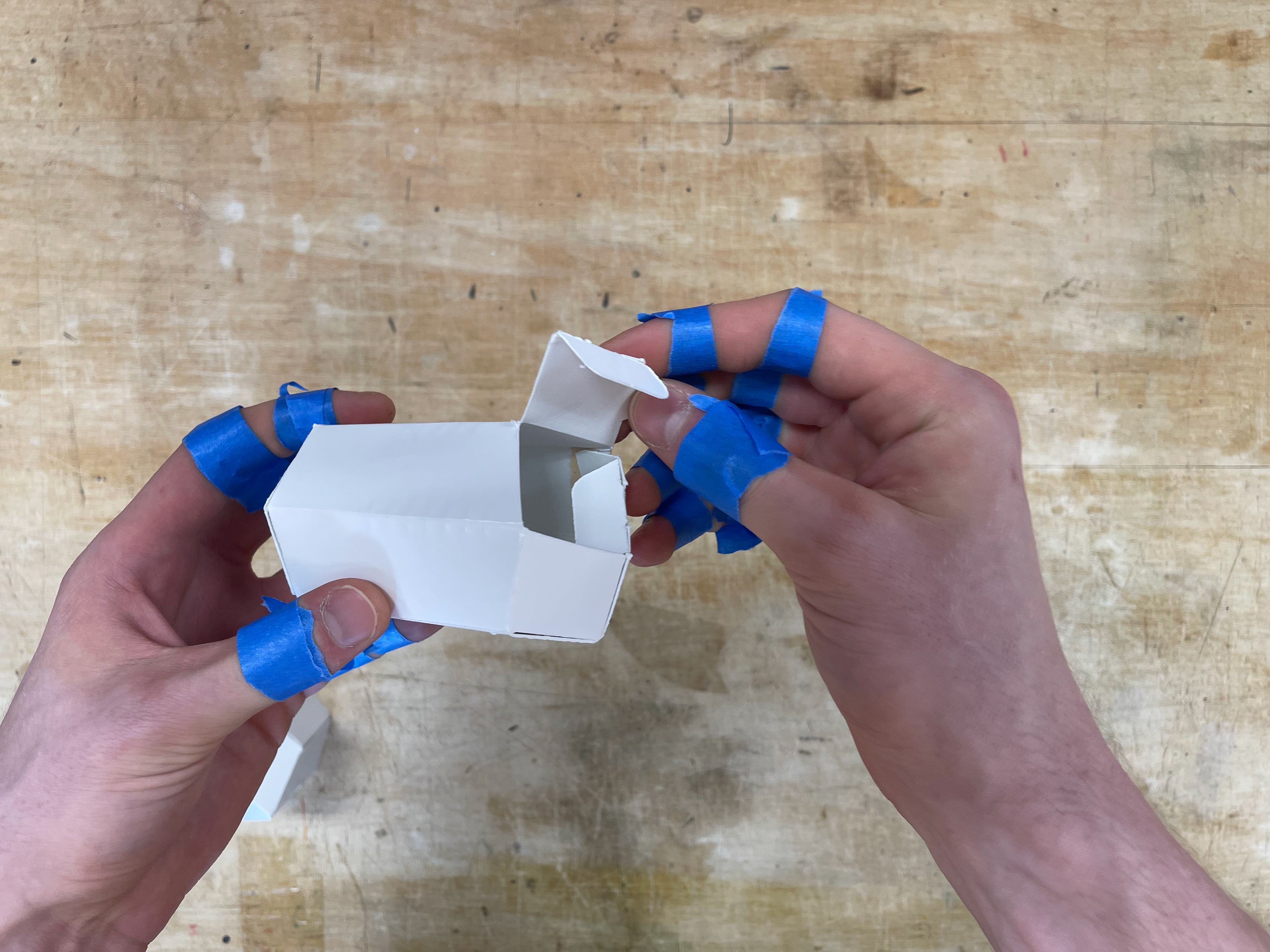
Dexterity Test
By taping the joints of our fingers, our team was able to replicate a similar feeling to that of someone with arthritis or weak hands. This allowed us to fully immerse ourselves in the lifestyle of our target demographic. This test lets us see if our FDA-compliant design was easy for someone within our consumer base to open without issue. After testing it multiple times, we concluded that our design was easy to use while still remaining effective.
.............
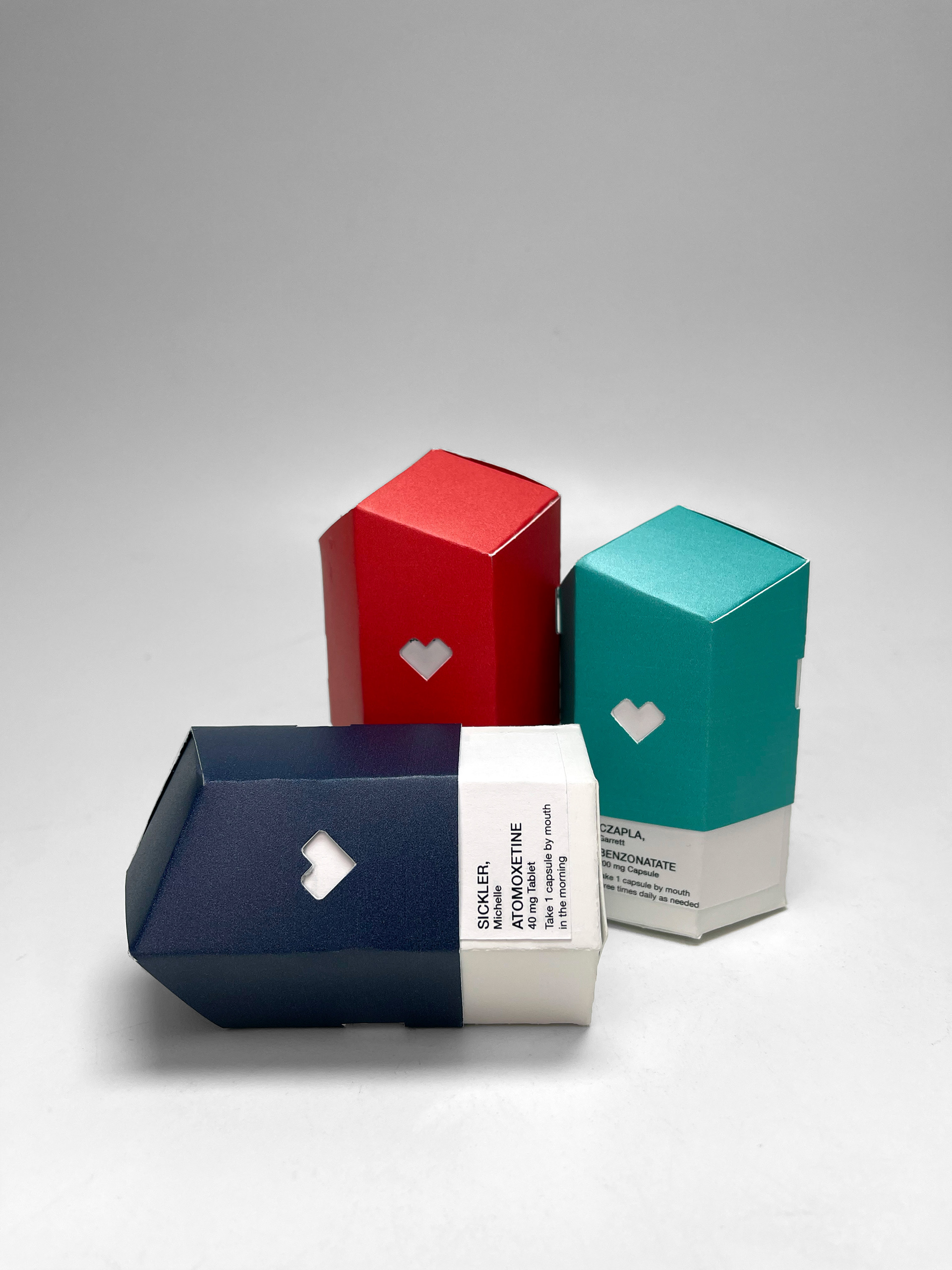
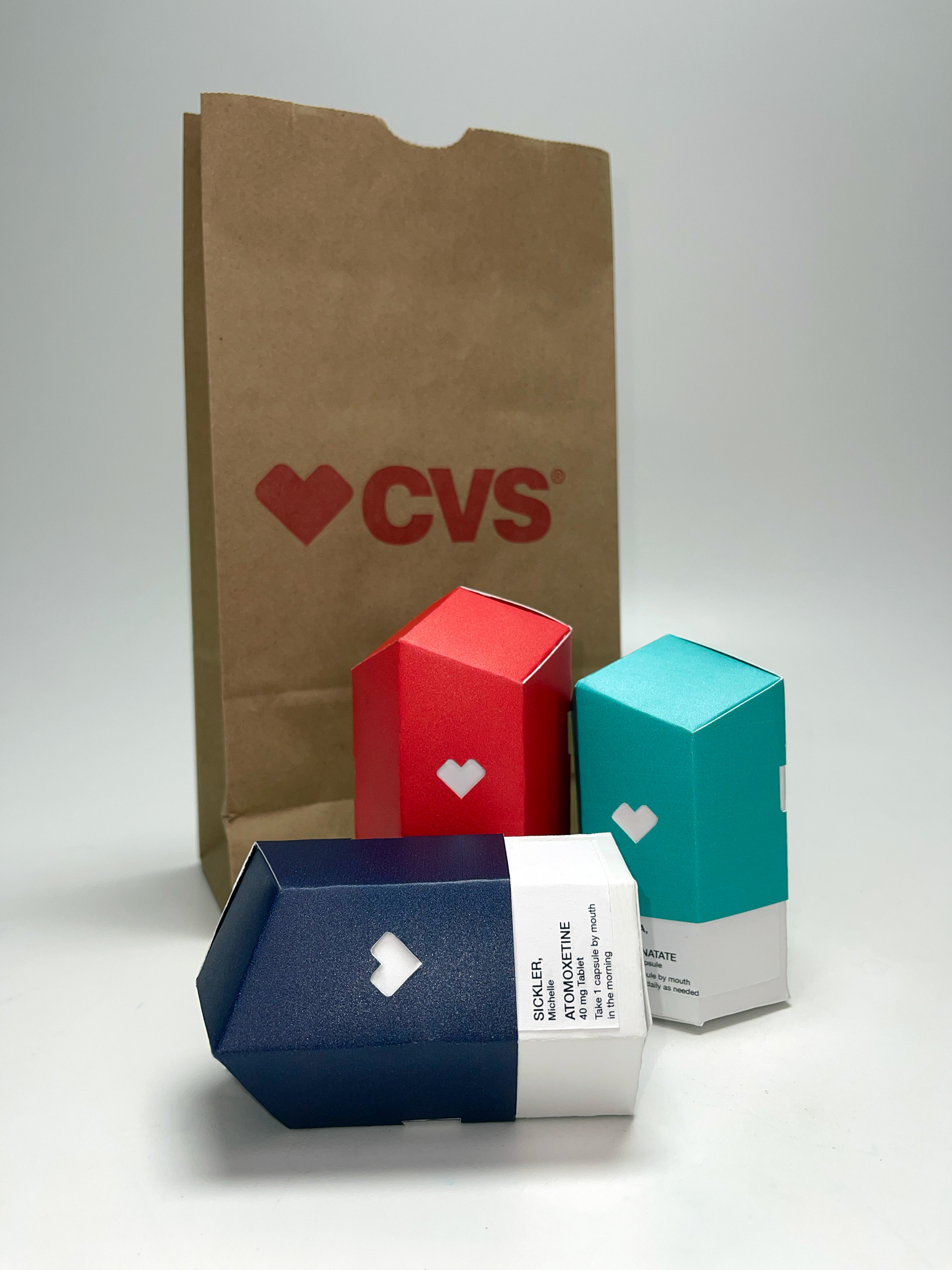
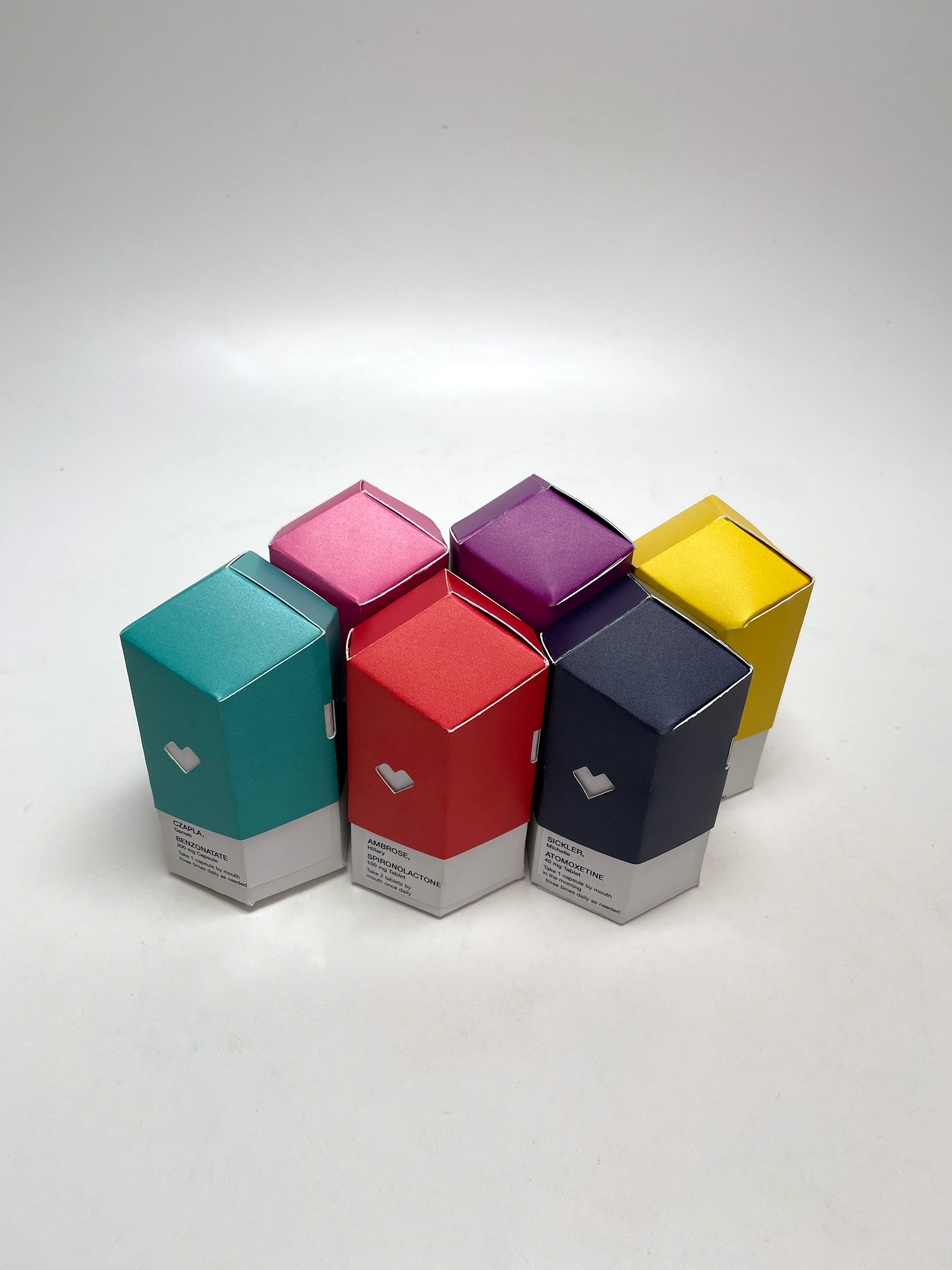
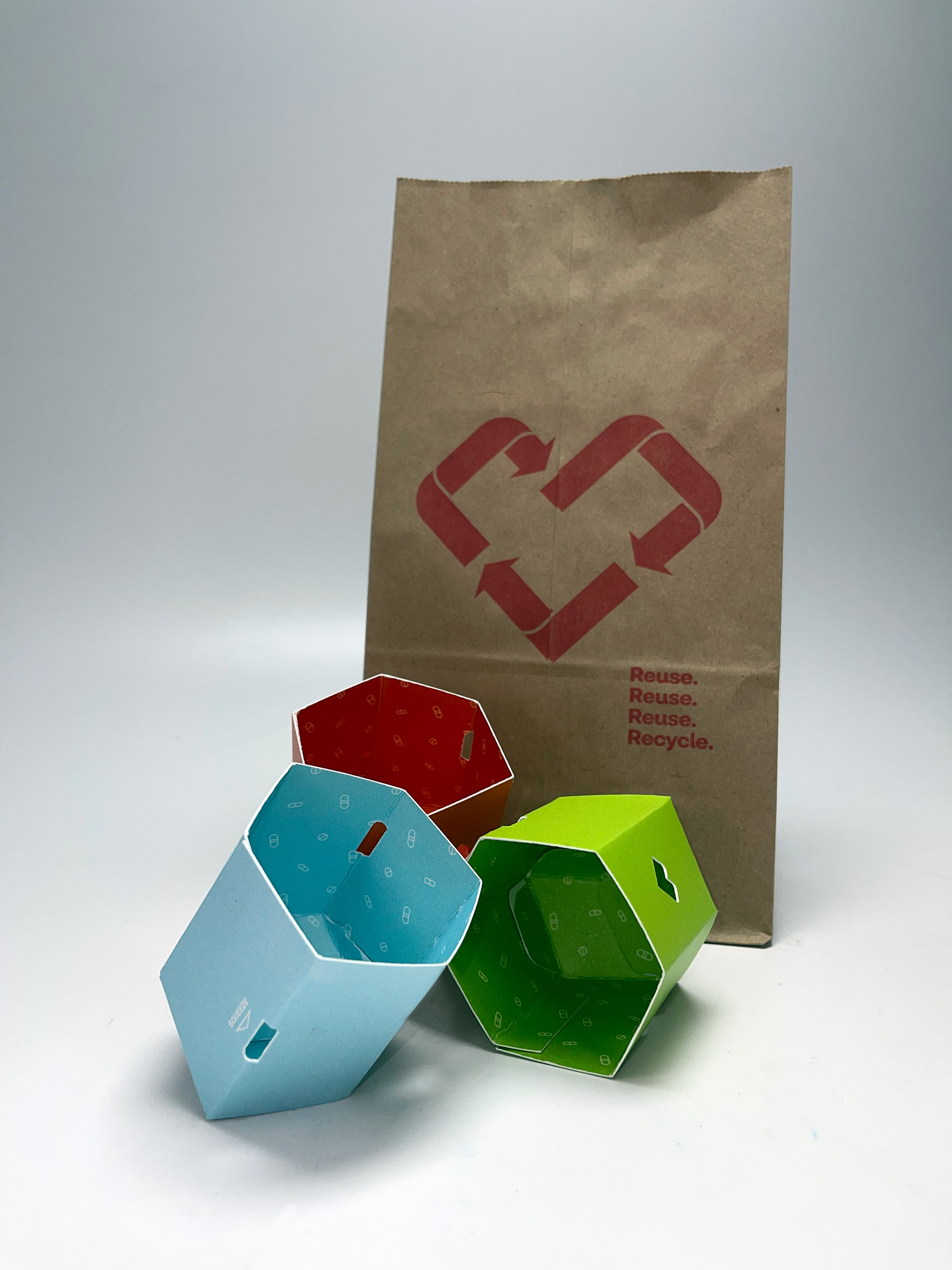
Overcoming Obstacles
The CNC machine we needed to cut out our prototype ended up breaking resulting in it tearing at our printouts. We had to hand-cut all of our samples with Exactos. This resulted in our final product not being as neat as we would have liked and us having to forgo some of the colored lids due to human errors.
Since we had a very short turnaround from receiving prints with only one shot to get everything right, we weren't able to do much user testing with the more finalized version of our product. We realized the "squeeze" spots could be better indicated visually and structurally.
We also noticed some of the color from the lids was rubbing off onto the white base container after being opened frequently. This was not something we initially considered but would need to be revisited.
.............
Curious to see more? View the process book here!